Hidden among the high-tech sensors, weapons, and other gadgets on display at the AFA Warfare Symposium in Aurora, Colo., earlier this month were a handful of bricks that could someday play a key role in how the military projects airpower in a future conflict.
The bricks were not made in a cement mixer. Instead, they were made with a biomanufacturing process where naturally-occurring bacteria converts road salt and an organic compound called urea into biocement, a hardened surface that may be able to take the weight of a landing or taxiing aircraft or a heavy ground vehicle. Using biocement to build a runway or road in a remote location could shave months of prep time and tons of equipment off the traditional methods.
“We’re trying to reduce or completely eliminate the need to bring in the heavy machinery, the concrete mixers, the literal boatloads of things that go into traditional construction, and being able to build it in a relatively quick timeframe,” Mitch Meade, an analytical chemist and deputy branch and program manager for the Air Force Research Laboratory, told Air & Space Forces Magazine.
Biocement is a promising technology at a time when the Air Force is pursuing the concept of Agile Combat Employment, where small teams launch and recover from remote or austere locations and can move quickly to new airfields. Part of the challenge of operating from smaller airfields is that there is not much space to land or park an aircraft.
“Some of them are pretty bare,” then-head of Pacific Air Forces Gen. Kenneth S. Wilsbach said in 2020. “And so what you might expect is, it’s a runway with a ramp. And that’s it.”
Wilsbach later said in 2023 that PACAF wants to clear jungles from overgrown World War II-era airfields to get at the concrete and asphalt buried beneath.
“We’re not making super bases anywhere,” he said. “We’re looking for a place to get some fuel and some weapons, maybe get a bite to eat and take a nap and then get airborne again.”
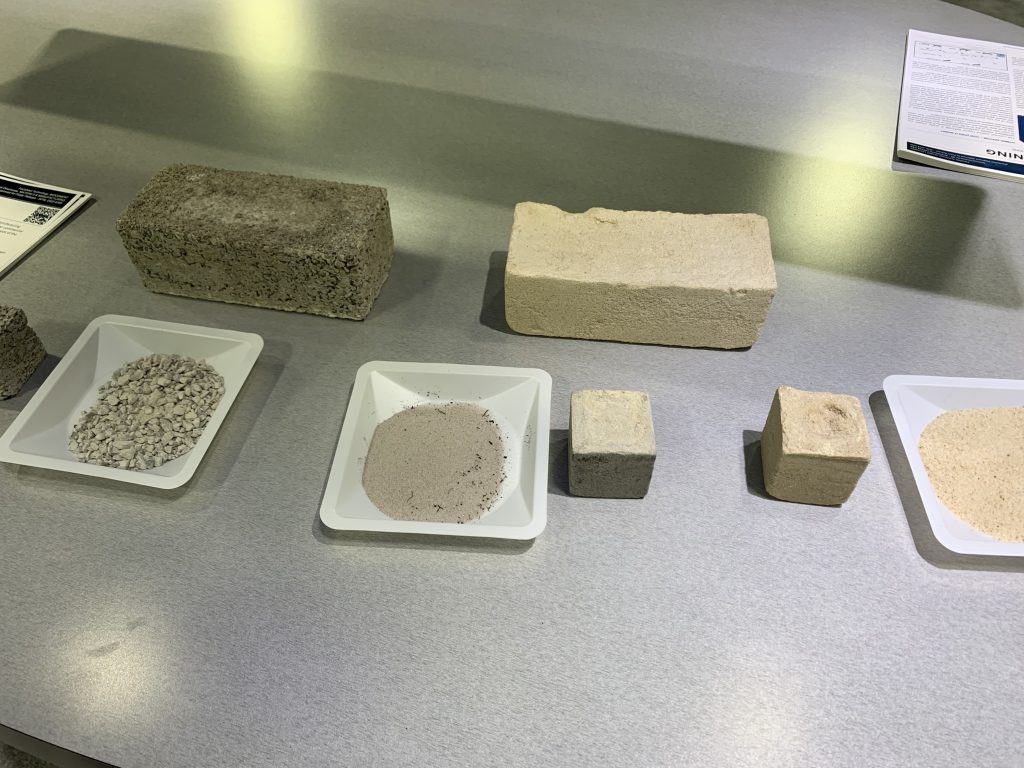
If the Air Force needs to expand runways, ramps, or roads, the usual process of making a paved surface may not be fast or lightweight enough to work in a Pacific conflict, where military airlift and sealift will likely be overburdened moving the rest of the force across the ocean.
“You almost have to build a cement factory and then all the infrastructure to lay down however much asphalt or concrete on top of that,” Meade explained. The process can take months.
Private companies have explored biocement for decades as a way to cut down on the carbon dioxide emitted by traditional cement production. It starts with S. pasteurii, a naturally-occurring bacteria that can be flown in or grown on site and is then sprayed onto the soil. Once it seeps into the ground, crews add calcium chloride and the organic compound urea. The S. pasteurii converts those ingredients into calcium carbonate, which binds the soil particles together into a hardened surface. The entire process takes less than 96 hours, though it can happen faster or slower depending on the soil and how often the bacteria is “fed.”
“Time is definitely the key factor,” Meade said. “We’re trying to build something as quickly as possible.”
The Air Force has been researching biocement since at least 2019. In the years since, landing pads made of biocement held up under CV-22s and a Navy MH-60S helicopter.
“Basically, you need an agricultural sprayer and some water tanks, so there is very little in materials you need to bring to the site,” Maj. MacKenzie Birchenough, a developmental engineer, said in 2019 about building a 2,500 square-foot prototype site with biocement.
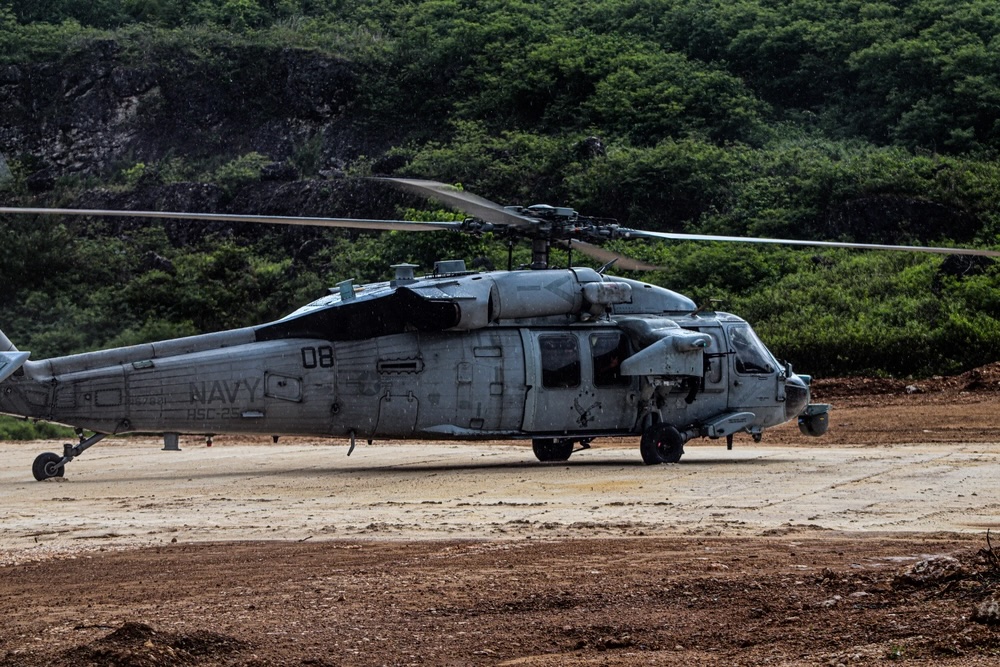
Tests with larger aircraft are still to come as AFRL works to “turn this from a biochemistry experiment into something an Airman could use,” Meade said. Researchers need to find out what kinds of soils, climate, and applications where biocement works best. Future tests will likely involve load carts, which can simulate the weight of an aircraft.
“This might be a great solution for one environment, but would something else work better in another environment?” the chemist asked. “Understanding where these things work best is a big part of the research we’re doing now.”
The goal is to answer those questions sooner rather than later, since military leaders are keenly interested in the technology.
“Any time you talk to a senior leader, their first question is ‘when are we going to see this in the field?’” Meade said. “Everyone we talk to, their imagination goes wild.”
Biocement is not meant to support a permanent airfield, but another advantage is that it does not require much clean-up. While calcium chloride does not dissolve, tillers can be used to turn the biocement back into native soil, which eliminates the need to dig up old concrete and ship it out. But could introducing a biocement-making bacteria have wide-reaching consequences?
“One question I get asked a lot is, when you put this stuff on the ground, will it turn the whole island into cement? Will it take over the world?” Meade said. “No, it will not take over the world.”