Boeing’s RVS 2.0 is getting closer to reality, but it’s still years away from delivery.
Upgraded cameras that can support refueling under covert conditions. A projection display incorporating a curved mirror to create a more immersive experience for boom operators. Enhanced processing power and new fiber-optic cabling. Boeing lifted the veil from its long-awaited Remote Vision System 2.0, offering a glimpse at enhancements for the KC-46 tanker, even as delivery of the new optical systems remains years away.
Boeing, Air Force, and Collins Aerospace officials shared the vision with a small group of reporters at Boeing’s Everett, Wash., facility in December, divulging a prototype RVS 2.0 display, diagrams detailing the planned system, and side-by-side video comparing the RVS 1.0 and 2.0 cameras. The video comparison suggests the new camera system overcomes the issues that plagued the original camera system, including blurriness and distortion, a lack of depth perception under certain conditions, and blackouts and whiteouts caused by sudden changes in lighting. Boeing funded the visit by Air & Space Forces Magazine.
Lt. Col. Joshua M. Renfro, from the Air Force’s KC-46 Cross Function Team, hailed RVS 2.0 as “the future” and a “quantum leap” in camera technology. But the Air Force and Boeing acknowledge that future is still far off. In October, they announced another 19-month delay, pushing operational use of RVS 2.0 to October 2025. By then, it will be more than five years after Boeing and the Air Force agreed on the plan for fixing the troubled Remote Vision System.
The dynamic range of these cameras is phenomenal. … They’re able to adapt to that changing environment.Boeing Test & Evaluation, chief boom operator Ernest Burns
RVS 2.0 must still complete its critical design review and win Federal Aviation Administration airworthiness approval. The preliminary design review was completed in April.
Details of what costs Boeing or the Air Force will bear also remain unclear. Boeing Vice President and KC-46 program manager James Burgess said only that the two sides have “reached agreements.” Burgess said the upgrade is “a much more advanced system for sure,” and noted that “computing technology has come a long way over the last 10 years.”
Cameras
The changes in RVS 2.0 start with the cameras on the boom itself and the panoramic camera on the fuselage. The original RVS used black-and-white cameras. Those on the boom were positioned at an angle, resulting in distortion at the edges of the image. The new system will have two, 4K color cameras. Distortion is eliminated and the change will not affect the aircraft’s mold line, officials said.
The new cameras will be able to adjust as needed to changes in light and shadow, ensuring operators see a clean, well-defined image, officials said. “The dynamic range of these cameras is phenomenal,” said Boeing Test & Evaluation chief boom operator Ernest Burns. “They’re able to adapt to that changing environment. Air refueling is always a changing environment. You never have the same conditions.”
That dynamic range means no more “whiteouts” or “blackouts” under difficult conditions. In addition, both the boom and panoramic views will also have upgraded Longwave Infrared (LWIR) cameras, able to detect and capture infrared radiation. Boeing calls this a “game-changer,” because it enables “covert refueling” without the use of visible light.
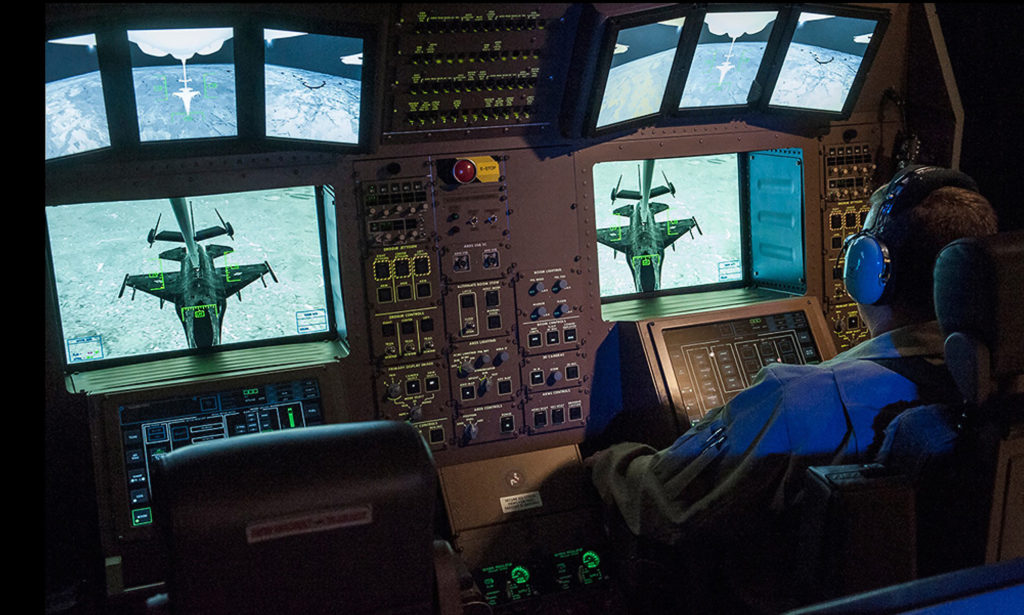
“If we tried to have external light, visible light on with the receiver coming up on vision goggles, it would bloom up the goggles, it just doesn’t work that way,” Burns said. “To have the boom operator wear night vision goggles and try to refuel, you would not have the depth perception required. They just don’t make night vision goggles with that kind of depth perception. So the best way to do that is to have LWIR cameras and a covert capability in the airplane with zero visible lights on using the LWIR cameras.”
Boeing officials shared video from the LWIR camera and let reporters wear night vision goggles to experience the KC-46’s infrared lights from the perspective of a receiver aircraft.
While the LWIR camera lacks some of the contrast and clarity of the color cameras, Burgess said the new LWIR cameras have three times the resolution of the original night-vision cameras, which Air Force officials have said lack the fidelity to conduct refueling operations in blackout conditions.
It’s not yet clear, however, if the Air Force will certify RVS 2.0 for covert refueling. There are still “operational restrictions” on the technology as it exists today, according to Boeing officials.
The Air Force has not yet validated the upgrades. “We have to see RVS 2.0 in the Air Force testing system,” Renfro said. “Boeing’s done a lot of work in that, but we haven’t seen on the Air Force side through developmental tests or IOT&E. So until we get to that point, I can’t really say what it’s going to deliver us in terms of combat capability. But we’ll put it through the paces, and I have every confidence it’ll bring us quite a bit.”
Better Vision
Improved image processing is part of the package. A second video processing unit, fiber optic connections, and a new, larger Aerial Refueling Operator Station (AROS) enhance the boom operator’s experience.
At the most basic level, what the screen operators will look at is larger and in color. Whereas the current system shows images smaller than their real-life size—about a 0.65-to-1 ratio—the new one will display at a 0.96-to-1 ratio, Burns said.
But it won’t just be a bigger screen. The monitor will be mounted higher and at an angle, facing the same way as the boom operator, who then looks at a curved mirror that reflects the image, wearing the same 3D glasses that operators use for the current system.
“What we have in 1.0 is a direct view. So you’re looking directly at an LCD monitor, which is projecting in 3D,” Burns said. The 2.0 version uses a projection system and a curved mirror to “reflect that LCD in three dimensions off of that mirror to provide that immersive experience for the operator.” The pay-off is more pronounced depth perception.
Boeing and Air Force boom operators “chose this type of design together,” Burns said. “We all looked at multiple different concepts: direct view, indirect view, projector, LCD, all of that. And we all came together, it was unanimous, really, we absolutely love this.”
The higher-mounted screen expands the space needed to accommodate the boom operator. Boeing is adding a center console between the two main operator seats, providing operators with more storage space, which they had asked for. To make room, Boeing and the Air Force agreed to remove a third seat from the station.
“It was a deliberate trade-off,” Burgess said. “Air Force engineers and operators said, ‘Hey, we’d rather have the added functionality in the AROS station than that third seat.’”
Other tweaks allow boom operators to adjust positioning of their seat and controls. Collaboration between the Air Force and Boeing teams has been exceptionally close, Burns noted. “We have been lockstep [since] Day One designing the AROS,” he asserted. ” It started literally with cardboard mock-ups, then we advanced to Styrofoam mock-ups, we cut out the panels in paper, and we literally pinned them on the Styrofoam mock-ups and redesigned how the station would look.”
Now as the they wait on FAA certification, the tanker team must also overcome supply chain issues. “A big part of the delay just had to do with availability of hardware … to build up the cameras and display boxes that are required for lab testing,” Burgess pointed out. “The hardware that goes into the lab, the electronics that go into the labs … it’s early versions of the hardware that go on an airplane. … It requires a pedigree of hardware to go into the lab that’s close to the pedigree required for flight, just because it’s all part of the chain of certification.”
With lab and flight-testing still to come and the actual fielding of the system several years down the road, several key details about RVS 2.0 remain unsettled, such as whether the Air Force will prioritize delivery of new KC-46s with the system or retrofits of already-fielded aircraft. Renfro said that question is still under consideration.
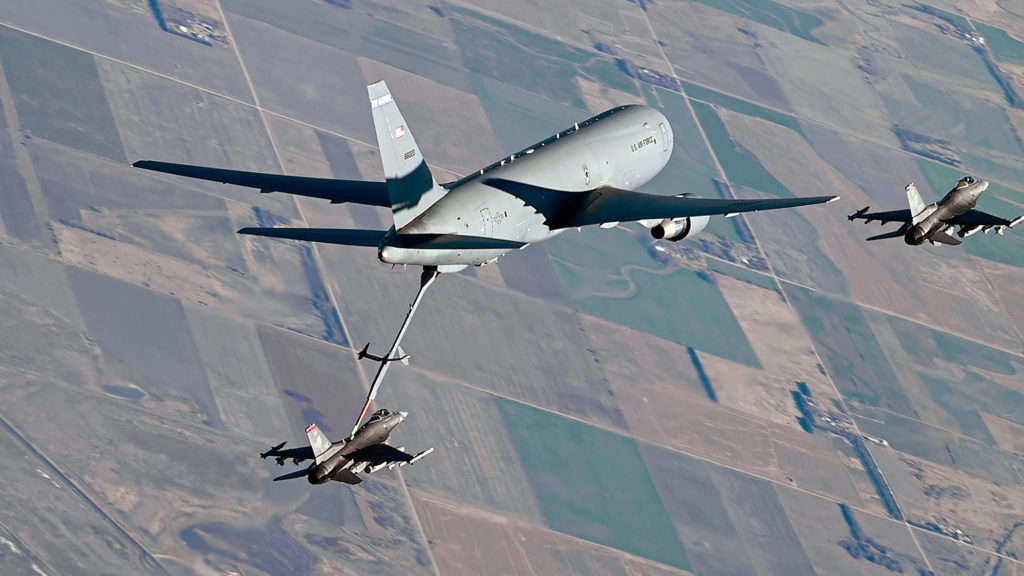
Meanwhile, boom operators have found workarounds to make RVS 1.0 effective, allowing Air Mobility Command to declare the aircraft ready for operational taskings worldwide. Those solutions won’t have an impact on the upgrade, however.
“RVS 2.0 is part of the long-term vision for this tanker. It’s where we need to be,” Renfro said. “I’m not going to presume to understand all of the pieces and parts that go into making it a reality. But I know that it will show up, and it will be amazing, and we’re going to employ it to the max extent possible. Until then, we’re going to keep using the KC-46 along the methods that we’ve used so far and give combat capability to the warfighter.”
Solving the Other KC-46 Deficiencies
While Boeing and the Air Force inch forward on the new KC-46 Remote Vision System 2.0, they are also making progress on other deficiencies that have thus far limited the aircraft in certain missions.
Boeing is tweaking the design of the actuator at the base of the tanker’s boom so that it will operate with the thrust-limited A-10 Thunderbolt.
The Pentagon Inspector General characterized the problem as a “stiff boom” that “would not extend or retract during flight-testing unless subjected to more force” than the A-10 could muster. Rather than a full “boom redesign,” Boeing KC-46 Program Manager James Burgess said the fix is a new actuator.
Speaking to reporters at Boeing’s Everett, Wash., plant, Burgess explained the challenge this way: The actuator “drives the boom out in the telescope direction, and then when a receiver connects with it, the receiver drives the boom back into sort of a nominal refueling position.” The original actuator requires about 1,400 pounds of pressure to enable refueling, Burgess said. But when at high altitude and fully loaded with weapons, the A-10 is “a very thrust-limited receiver aircraft; it had trouble pushing it up to that 1,400 pounds and then keeping it compressed at that force.” Indeed, A-10 attack aircraft still cannot refuel from the KC-46, even after Air Mobility Command announced in September that the KC-46 had been cleared for worldwide deployments and combatant commander taskings.
The new actuator will be able to better regulate the force needed. Boeing shared a 3D model of the new design in the boom assembly facility.
“What it does is control force as a function of rate, so as the receiver pushes harder on it, it pushes back harder on the receiver,” Burgess said. “If the receiver doesn’t push as hard on it, it doesn’t push as hard back. So it’s a little bit more conducive to lightweight, thrust-limited receivers like the A-10.”
The new actuator is smaller than the current one, and simpler, as well, with only one torque motor rather than two.
“It turns out [the current actuator] was probably a little overdesigned initially in terms of redundancy,” Burgess said. “That has nothing to do with the deficiency. But Boeing and the Air Force worked together to take advantage of simplifying the design as part of the redesign. The relief manifold assembly … goes away, and it’s replaced with what’s called a PQ valve.”
A working version of the new actuator is currently going through lab tests at Boeing Field in Seattle, Burgess said. Delays, however, continue to mount: An Air Mobility Command spokesperson told Air & Space Forces Magazine in November that the fix, referred to as the Boom Telescoping Actuator Redesign (BTAR), “is experiencing delays due to issues getting a compliant actuator from Boeing’s subcontractor, Moog.”
AMC said its most recent projection has flight-testing ending in late 2023, with retrofits for the existing fleet starting in late 2025. Delays could push that still further into the future.
The “stiff boom” is just one of several non-RVS deficiencies in the KC-46 identified by the Air Force. Another is related to leaks in the fuel system that were first identified in March 2020. Reports indicated seals designed to “flex” and move with the aircraft were insufficient to the task. Burgess said the problem was due to the difficulty of installation, and that Boeing has since redesigned the valve seals to make it easier to install them. As a result, “far fewer” fuel leaks have been reported, Boeing and Air Force officials noted during the plant visit.
Officially, the leaking seal deficiency has not yet been resolved, but Burgess said that was more of a formality at this stage, the result of infrequent meetings of the KC-46 deficiency board.
Other deficiencies have been resolved. Burgess touted during the tour the redesigned cargo pallet lock, which now includes a safety feature to ensure the lock stays fully engaged. The previous design sometimes unlocked when twisted during flight, leading the Air Force to restrict the aircraft from carrying cargo or passengers for a few months in 2019.
All in all, Air Force officials projected optimism, both in the KC-46’s current capabilities and the future fixes coming.
“If we had to go to war today, we would take this airplane with us,” Lt. Col. Joshua M. Renfro, from the Air Force’s KC-46 Cross Function Team, told reporters. “And we’d be fantastically confident in its capabilities in order to deploy it. However, long term, there’s always things that we can leverage—emerging technologies, and that partnership [with Boeing]—to acquire what the long-range vision for this tanker needs to be.”