A prototype aircraft tug being tested out at Holloman Air Force Base, N.M., could save MQ-9 Reaper maintainers time and money and cut down on safety risks on the flightline.
The TowFLEXX is a remote-controlled, electric tug that has a smaller logistical footprint and takes up less space than old-school aircraft towing systems, which often involved specialized tractors or a gas-powered truck and a towbar. A smaller footprint would help with Agile Combat Employment, the Air Force strategy of dispersing teams of Airmen to smaller or austere air bases to complicate targeting for near-peer adversaries such as Russia and China.
“Typically you would take up two or three pallet positions with the older version of a tow vehicle,” Tech. Sgt. Dwane Parmelee, with the Holloman-based 49th Component Maintenance Squadron, told Air & Space Forces Magazine. “This would take up one pallet position at most, and you can still stack bags and stuff on top of it, so you’re really getting a dual-purpose pallet position there.”
While other Air Force bases also use TowFLEXX, the prototype at Holloman are special. Unlike their counterparts, the TF3 variant is equipped with a Light and Detection Range (LiDAR) collision avoidance system which spots obstacles and automatically stops the tug. That means fewer Airmen have to be on hand to supervise a towing operation.
Under the old system, towing a Reaper might take five to six Airmen, Parmelee explained: one to operate the towing vehicle, three or more wing and tail walkers to make sure the 66-foot-wide, 36-foot-long aircraft doesn’t hit anything, and a supervisor overseeing the operation. With the TF3, that number falls to just the vehicle operator and two wing walkers, which frees up maintainers to do other tasks.
“Every hour we save an Airman from doing a job that technology can do, that’s saving us time and it’s saving us money,” said Senior Master Sgt. Joseph Anger, quality assurance superintendent for the 49th Maintenance Group. “We’re looking at saving over 3,000 hours per year just towing the MQ-9 alone at Holloman.”
That would more than make up for the TowFLEXX’s price tag—between $50,000 and $90,000, depending on the variant—at a time when many Air Force bases have too few maintainers to sustain an aging fleet of aircraft. Besides cost-savings, the LiDAR-equipped TF3s could also increase flightline safety by preventing collisions.
“Humans, we’re really good, but we could be working an eight-hour shift in the rain or something like that and something happens,” Anger said.
At a recent demonstration, the TF3 avoided engineers from Evitado Technologies, the company that built the LiDAR anti-collision system, who served as obstacles in the tug’s path. Some maintainers “were shocked by the LiDAR system’s ability to identify obstacles inches away from the aircraft and then shut down,” Anger said.
“Everyone was amazed,” he said. “They were coming up like ‘hey, what else can we put this on?’”
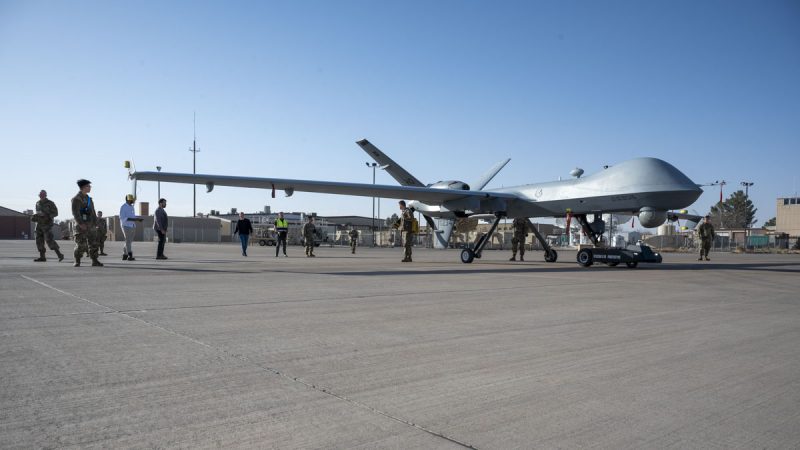
Also impressive was the tug’s maneuverability: without a towbar expanding its turning radius, the TowFLEXX spun the Reaper in circles in place, which could help Airmen store more aircraft and equipment in tighter spaces. And while the older TowFLEXX models had just one motor, the TF3 has two, which means it can tow heavier aircraft.
In 2023, there was “an upward trend” in ground mishaps involving maintenance, aircraft towing, and other flight line work, Maj. Gen. Sean M. Choquette, the Air Force Chief of Safety, said in October. TF3 may be able to help with that.
“You have a 360-degree view of the aircraft and any obstructions,” said Parmelee. “Therefore your mishap prevention is going to improve astronomically.”
Anger sees a future where the LiDAR-equipped TowFLEXX can tow an aircraft completely autonomously.
“My overall goal is to have these TowFLEXXes just pull up to the aircraft, connect to the aircraft, and then tows without anyone being there,” he said.
Grassroots Innovation
Perhaps just as helpful as the TowFLEXX is the story of how the TF3 prototype got to Holloman. Anger has a history of liaising between flightlines and tech companies to make Airmen’s jobs easier. A key tool for doing that is AFWERX, an Air Force program that provides funding and technical expertise to support grassroots solutions to Air Force and Space Force challenges.
Through AFWERX, Anger learned how to access small business innovation research contracts, which helped him “push a lot more ‘outside-the-box’ thinking,” and he encouraged other Airmen to do the same.
AFWERX is there “to help the innovator at the wing level, or even at the squadron level or below, come up with grassroots innovations,” he said.
Anger had worked with Evitado in the past, which helped spark the idea to partner with TowFLEXX. Now he wants to move fast to get the project through the “Valley of Death,” the transition period between prototype and scaled-up production where many ideas fizzle out.
More cash from the Strategic Funding and Tactical Funding programs should help with that; Anger said those funding buckets and support from leadership has helped more projects get out of the valley.
“Hopefully in the near future we could be replacing the older systems with this new autonomous system,” Anger said.
“The more Airmen have a voice in innovation, the better,” the senior master sergeant said. “We have a lot of great technology that we’re working on, and we’re going to be able to save money, save time, and improve quality of life for Airmen.”
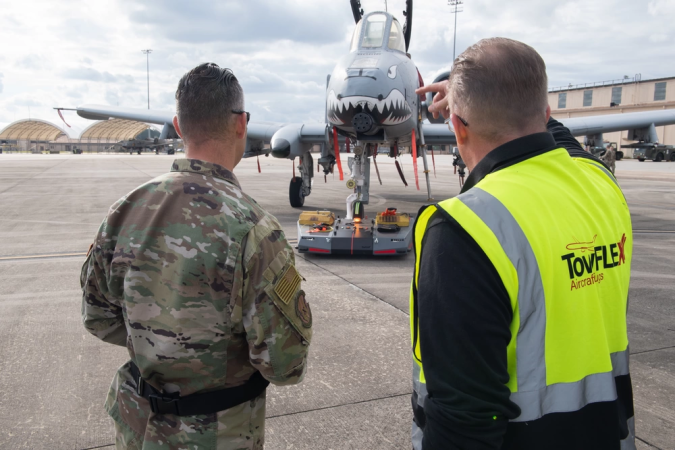