High-Altitude, Low-Opening (HALO) parachute jumpers from Air Force Special Operations Command are sporting new headbands, woven from advanced fibers that measure and report the wearers’ vital signs, transmitting the data to a tablet or other device nearby.
“We can measure body temperature, heart rate, and SpO2 [blood oxygen saturation] and wirelessly transmit that data to the team leader,” said Alexander “Sasha” Stolyarov, CEO of Advanced Functional Fabrics of America (AFFOA), a Defense Department-supported nonprofit manufacturing innovation institute.
It’s potentially life-saving information for HALO jumpers, who can suffer from hypoxia and hypothermia due to the intense cold and thin air at high altitudes.
It’s also the product of “a beautiful marriage” between the Department of Defense and the private sector, said Tracy Frost, director of the DOD’s Manufacturing Technology Program.
To be clear, explained Stolyarov, there is no widget buried in the headband.
“We integrated the sensors in a distributed way within the fabric that makes up the headband itself,” he said. “So if you’re looking at the headband, it looks just like a regular headband. It stretches and twists.” But that fabric, and some flexible plastic strips inside, comprise the sensors that actually do that measuring—emitting the light and detecting it bouncing back at different wavelengths—the chip that does the computation, and the antenna that sends it wirelessly to the tablet.
“It’s all in the fabric,” he said.
That gives the headband, worn unobtrusively underneath the HALO jumper’s helmet, a big edge over wristwatch-type wearables which suffer from “user friction” and can be rendered inaccurate by the wrong kind of movement.
An official with Air Force Special Operations Command confirmed HALO jumpers had tested the prototype headband but declined to comment further.
The HALO jumper headband is just one of a slew of new clothing items made possible by advanced functional fabrics. (Stolyarov doesn’t like the term “wearables” because of the clumsy plastic items that phrase brings to mind).
Advanced clothing can do more than gather data; it can also respond, Stolyarov said.
Because Air Commandos need nimble fingers, they often eschew the kind of thick gloves needed in extremely cold temperatures. AFFOA has prototyped a sleeve worn over the forearm that reacts to extreme cold by warming, raising the temperature of the blood before it reaches the fingers. It also makes thinner, less constricting gloves more feasible, he said.
But that’s just the beginning.
Fabric that can sense and respond could help protect pilots, compressing or expanding to help ensure proper blood flow during high-G maneuvers.
“Imagine a T-shirt that provides you and your healthcare provider with real-time meaningful information about how you’re doing in the real environment,” he said. “But you don’t feel like you’re being interrogated by medical equipment. You’re just wearing a T-shirt that you can actually throw in the laundry. … That kind of user adoption is what I think we’ll get to in five to 10 years.”
Further into the future, Stolyarov predicted that clothing could be designed to deliver treatment on the fly. “If the data tells me my wearer is sick, maybe I need to inject some drugs. That’s the next level. … You’re really talking about completely new materials that then enable completely new applications,” he said.
AFFOA is one of nine Department of Defense-sponsored Manufacturing Innovation Institutes scattered across the country.
Another six are sponsored by the Department of Energy, and the Department of Commerce sponsors a 16th—all focused on different technology areas.
The nine DOD-sponsored institutes cover industries from AFFOA’s textiles to digital manufacturing, design/automation and robotics, and biotechnology, said Frost.
They were established in the 2010s with a two-fold purpose: To try and rekindle domestic manufacturing, which since the 1990s has outsourced most textile work to low-labor cost countries; and to focus on high-value, high-tech production. By doing so, the U.S. military ensures it can rely on a domestic supply chain, especially for cutting edge technology products.
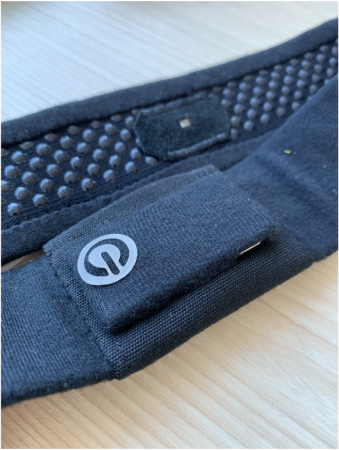
The institutes straddle the uncomfortable new reality of 21st century technology, where commercial, consumer-driven innovation, because of its scale, can outpace government-led efforts to develop technologies for national security.
Frost said the institutes always strive to facilitate the development of technologies that are dual use: Developed to solve a national security problem, but useful in addressing the much larger consumer market.
“They’re a beautiful marriage between addressing defense needs and addressing commercial needs and marrying up Department of Defense needs with commercial interest in developing new product lines and continuing to innovate,” she said. “There’s a big recognition that working together doubles our investment and our chances of reaching success in transitioning these technologies.”
The United States lost almost one-third of its manufacturing jobs between 2000 and 2010. More than 64,000 factories closed, manufacturing capital investment and output suffered, and the productivity rate dropped.
By 2016, when AFFOA was founded, “we had really lost our manufacturing base in textiles, because [since the beginning of the century] a lot of that work started going overseas to lower labor cost countries like China and other East Asian countries,” explained Stolyarov.
It would be pointless to chase that low-value production, he added, so AFFOA set out to create a U.S. textile manufacturing base “differentiated based on technology. And what that means is having unique capabilities, being able to produce fibers and fabrics that no one else in the world knows how to produce.”
The U.S. already led the world in laboratory-level capabilities, Stolyarov said—in addition to fabrics that can store data and do computation, its universities are able to synthesize “fibers that can change color, fibers that can store energy. There are fibers that can detect chemical and bio hazards.”
U.S. universities had already produced fibers and fabrics that demonstrated all these capabilities, he said.
“Where we’ve struggled [as a nation] is in translating that into a manufacturing base, getting from the lab to the factory floor. … [In 2016] no one had actually shown that you can produce these things on industrial manufacturing equipment,” he said.
AFFOA and the other innovation institutes were set up to bridge that transition, Stolyarov said. “In a nutshell, we set out to work with our manufacturers to transition innovations that are taking place in academia or even maybe startups that are wanting to create companies out of those innovations, and help those founders and help those manufacturers harness the innovation that’s taking place here to create a manufacturing base.”